اطلس کوپکو
خشک کن جذبی سطحی هوا برای بهترین راندمان
CD+ series (330-1400 l/s, 700-2968 cfm)
AD+ series (330-3000 l/s, 700-6360 cfm)
BD+ series (330-3000 l/s, 700-6360 cfm)
XD+ series (550-3600 l/s, 1165-7629 cfm)
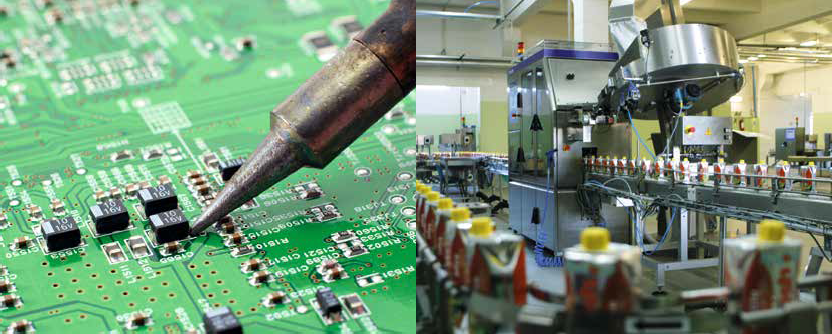
COMPLETE PROTECTION FOR YOUR APPLICATION
Dry and clean compressed air is essential for a broad range of industrial applications. Yet it must be produced reliably, energy-efficiently and cost-effectively. Atlas Copco’s desiccant dryers protect your systems and processes. Their robust design ensures they operate with total reliability and deliver a constant, stable dewpoint in full load conditions and even during a temporary overload.
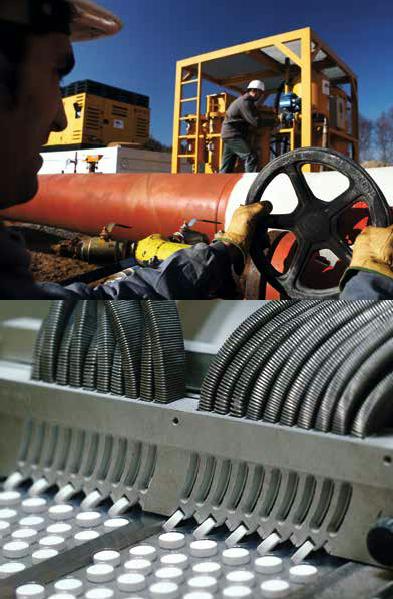
Electronics
Food & Beverage
Oil & Gas
Pharmaceuticals
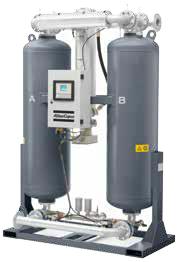
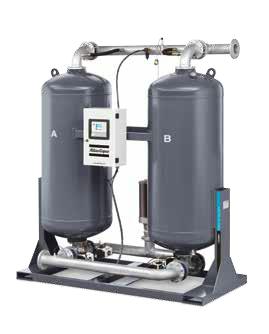
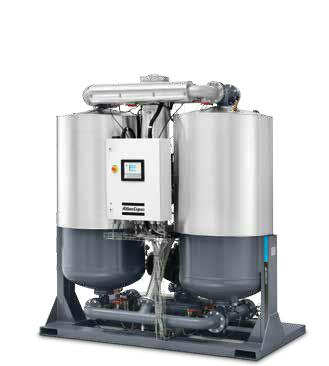
Protecting your reputation and production
Highest reliability
Add Your Heading Text Here
Easy installation and long maintenance intervals
HOW DOES A DESICCANT DRYER WORK?
- Heatless dryers use only compressed air as purge
- Heated purge dryers use a combination of compressed air as purge and heat
- Blower dryers use a combination of air from an external blower and heat.
- Heat of compression dryers use the heat of the
The drying process
- Wet compressed air flows upward through the desiccant which adsorbs the moisture, from bottom to top (1).
The regeneration process
Heatless desiccant dryers:
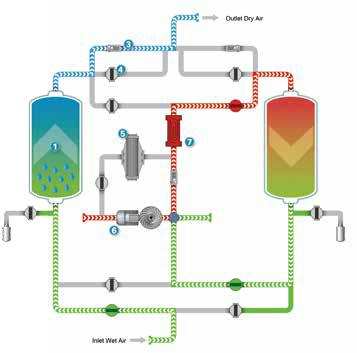
- Dry air from the outlet of the drying tower is expanded to atmospheric pressure and sent through the saturated desiccant, forcing the adsorbed moisture out (2) (4).
- After desorption, the blow-off valve is closed and the vessel is re-pressurized.
- Dry air from the outlet of the drying tower flows over an electric After heating it is expanded to atmospheric pressure and sent through the saturated desiccant, forcing the adsorbed moisture out (2) (4).
- After desorption, the blow-off valve is closed and the vessel is re-pressurized.
Heated purge desiccant dryers:
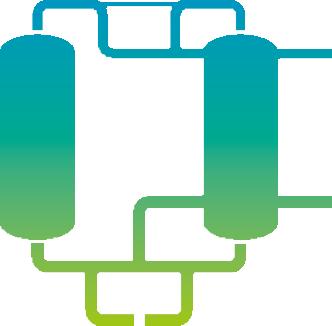
Heated purge desiccant dryers:
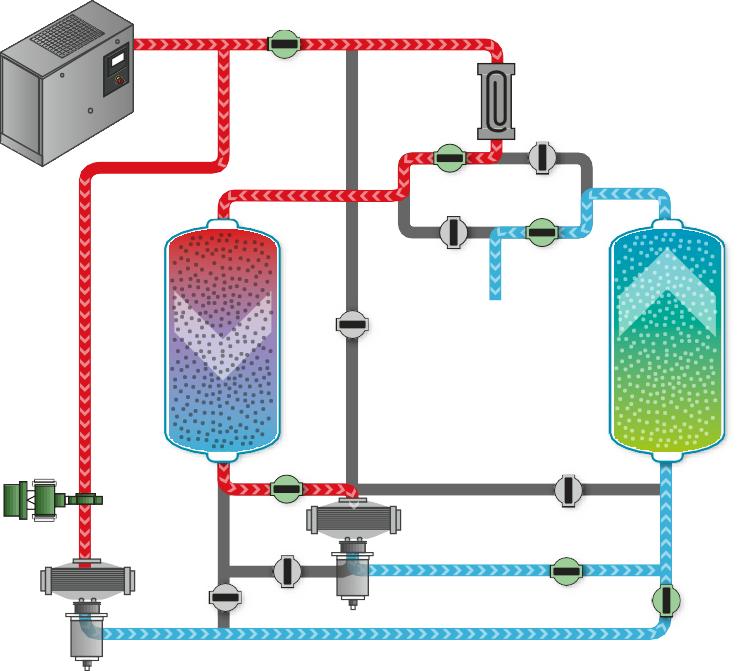
- Dry air from the outlet of the drying tower flows over an electric After heating it is expanded to atmospheric pressure and sent through the saturated desiccant, forcing the adsorbed moisture out (2) (4).
- After desorption, the blow-off valve is closed and the vessel is re-pressurized.
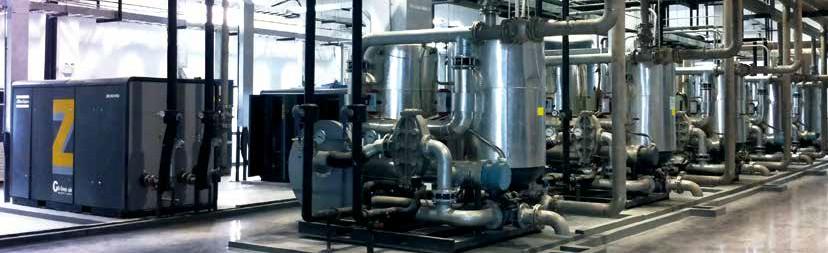
Heated blower desiccant dryers (purge cooling or zero purge cooling):
- The blower (5) takes ambient air and blows it over the external heater (6). The heated air is then sent through the saturated desiccant (2), forcing the adsorbed moisture out, from top to
- Purge: After the heating, the hot tower desiccant is cooled. Cooling is done by expanding dry compressed air from the outlet of the adsorbing vessel over the hot reactivated tower, from top to bottom
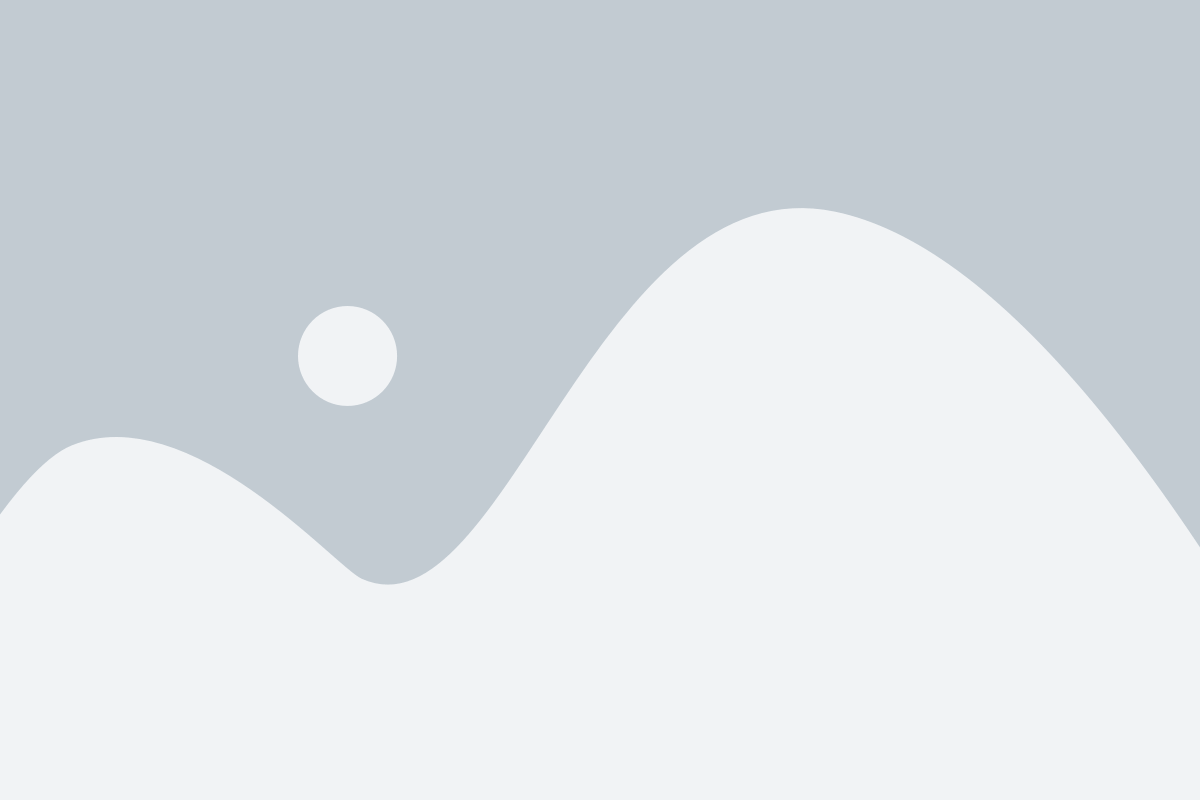
Zero purge cooling:
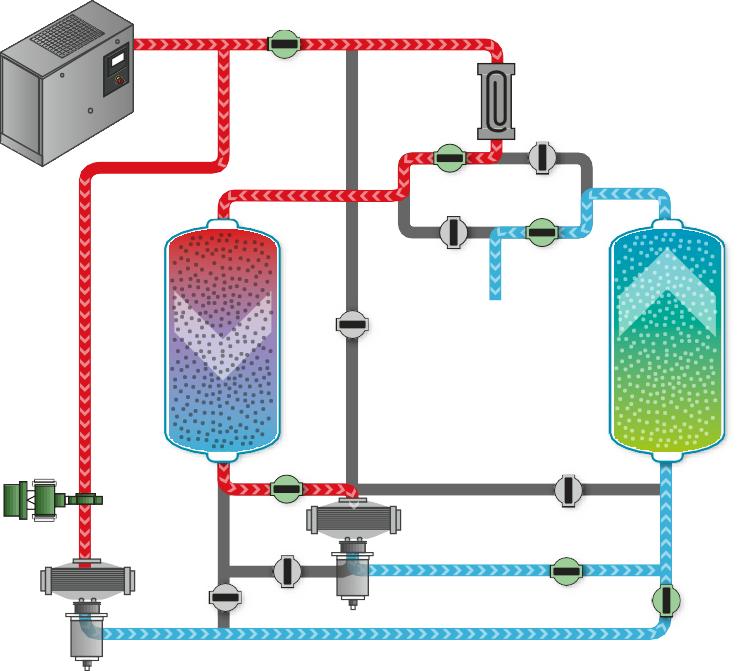
- Purge: After the heating, the hot tower desiccant is cooled. Cooling is done by expanding dry compressed air from the outlet of the adsorbing vessel over the hot reactivated tower, from top to bottom
Switching
- After regeneration, the functions of both towers are switched (3).
Atlas Copco’s XD+ adsorption dryers use the heat of compression from oil-free compressors to dry compressed air. This heat is used effectively to regenerate the high quality desiccant, significantly reducing energy and operating costs. As any need for outside energy supply can be eliminated, adsorption is by far the most economical method of compressed air drying
Heat of compression desiccant dryers (with zero purge cooling)
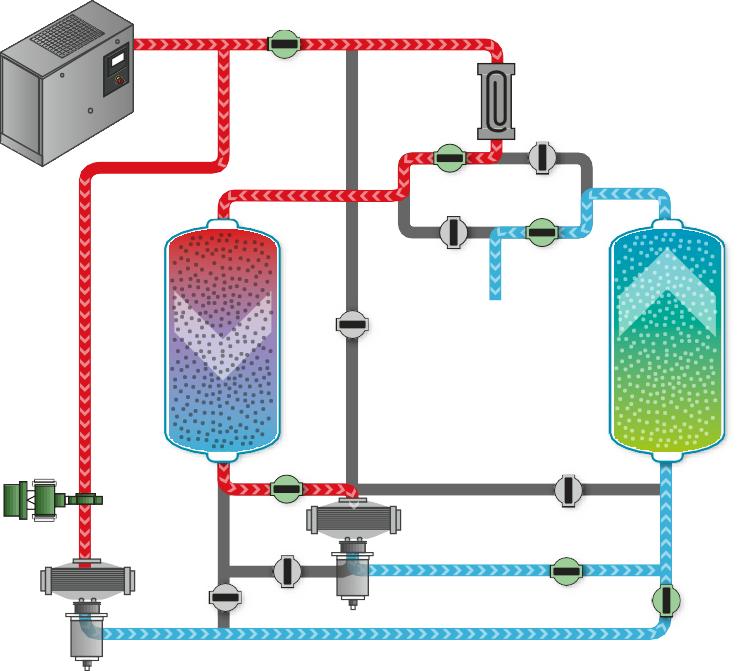
A wealth of possibilities:
XD+-S models
Both models are available as single inlet and double inlet variant.
Use the heat of compression for regeneration and feature dewpoints of -10°C to -20°C, dependent upon ambient conditions. When combined with the high outlet temperatures of a ZR compressor, XD+-S Purge models can achieve a dewpoint of -40°C
XD+-G models
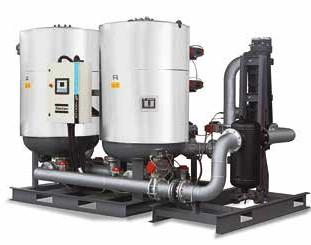
SUPERIOR ENERGY-EFFICIENCY
A dryer’s energy consumption mainly goes to internal pressure drops and the regeneration process. The key for designing desiccant dryers is therefore to keep the pressure drop as low as possible, and to develop technologies that allow regeneration to be as efficient as possible. Atlas Copco’s dryers are designed to have a very low internal pressure drop, and provide the most efficient regeneration process.
Lifecycle cost
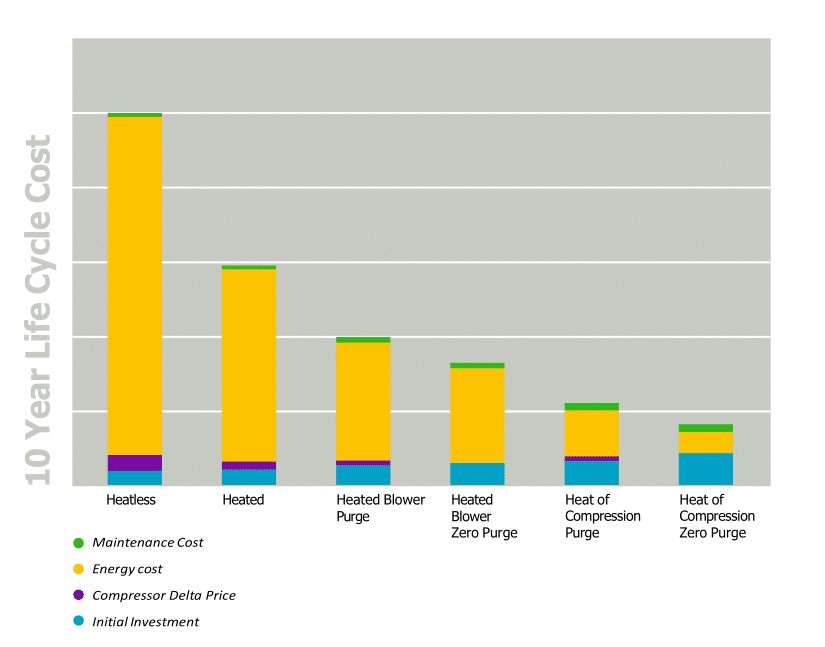
Efficient regeneration due to Dewpoint Dependent Switching
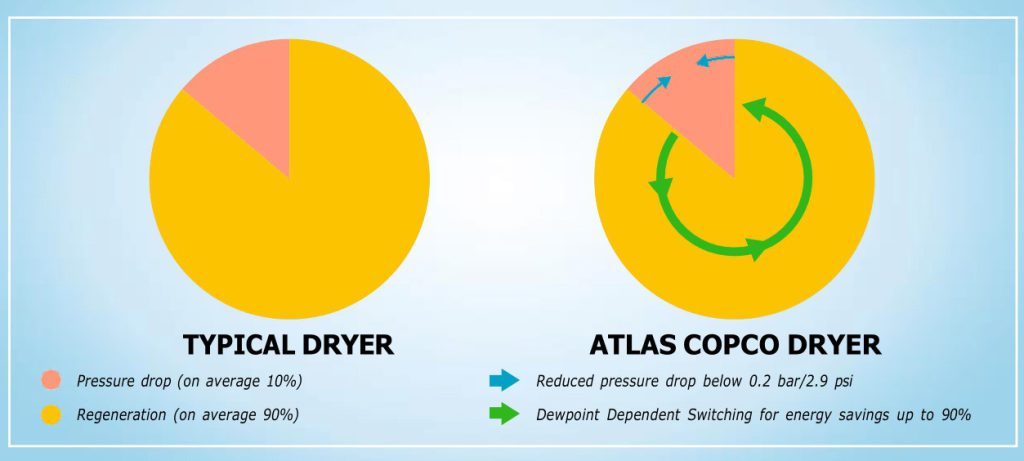
CD 330+-1400+:OUTSTANDING RELIABILITY AND AVAILABILITY
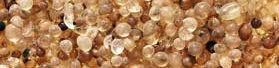
Long-life silica gel desiccant
- High-adsorption silica gel desiccant needs less reactivation energy than other drying agents.
- 2-layer desiccant bed; a water-resistant bottom layer protects the high- performing top
- Pressure dewpoint of -40°C/-40°F as standard (-70°C/-100°F as option).
- Up to 30% extra desiccant overfill to deliver consistent performance even in harsh conditions such as high temperatures and temporary
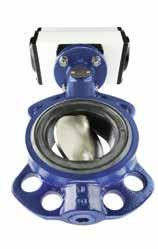
Stainless steel valves
Fully stainless steel high-performance butterfly valves with actuators ensure long lifetime.
Low-wattage density heater
- Stainless steel design ensures long
- Nickel-plated heater pipe protects against
- Heater is installed in an insulated heater pipe for most energy- efficient
- Optionally insulated vessels are available to further reduce heat losses and increase overall efficiency (standard on the -70°C/-100°F variant).
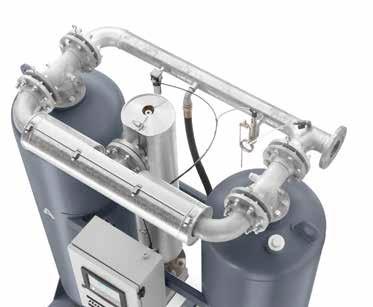
Galvanized piping with flanged connections
Flanged piping simplifies maintenance and minimizes the chance of leakage. Pipe sizing is optimized to ensure a low pressure drop, resulting in energy savings.
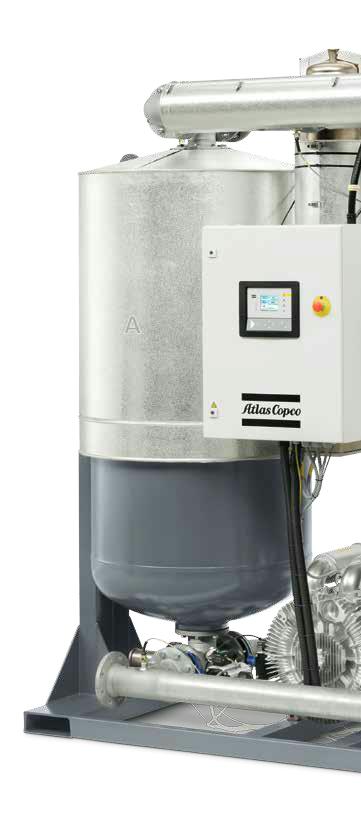